Related Jobs
View all jobsGroup Project Manager
Document Control Manager
Environment & Consents Manager
Senior Design Manager
Commercial Manager

Subscribe to Future Tech Insights for the latest jobs & insights, direct to your inbox.
Industry Insights
Discover insightful articles, industry insights, expert tips, and curated resources.
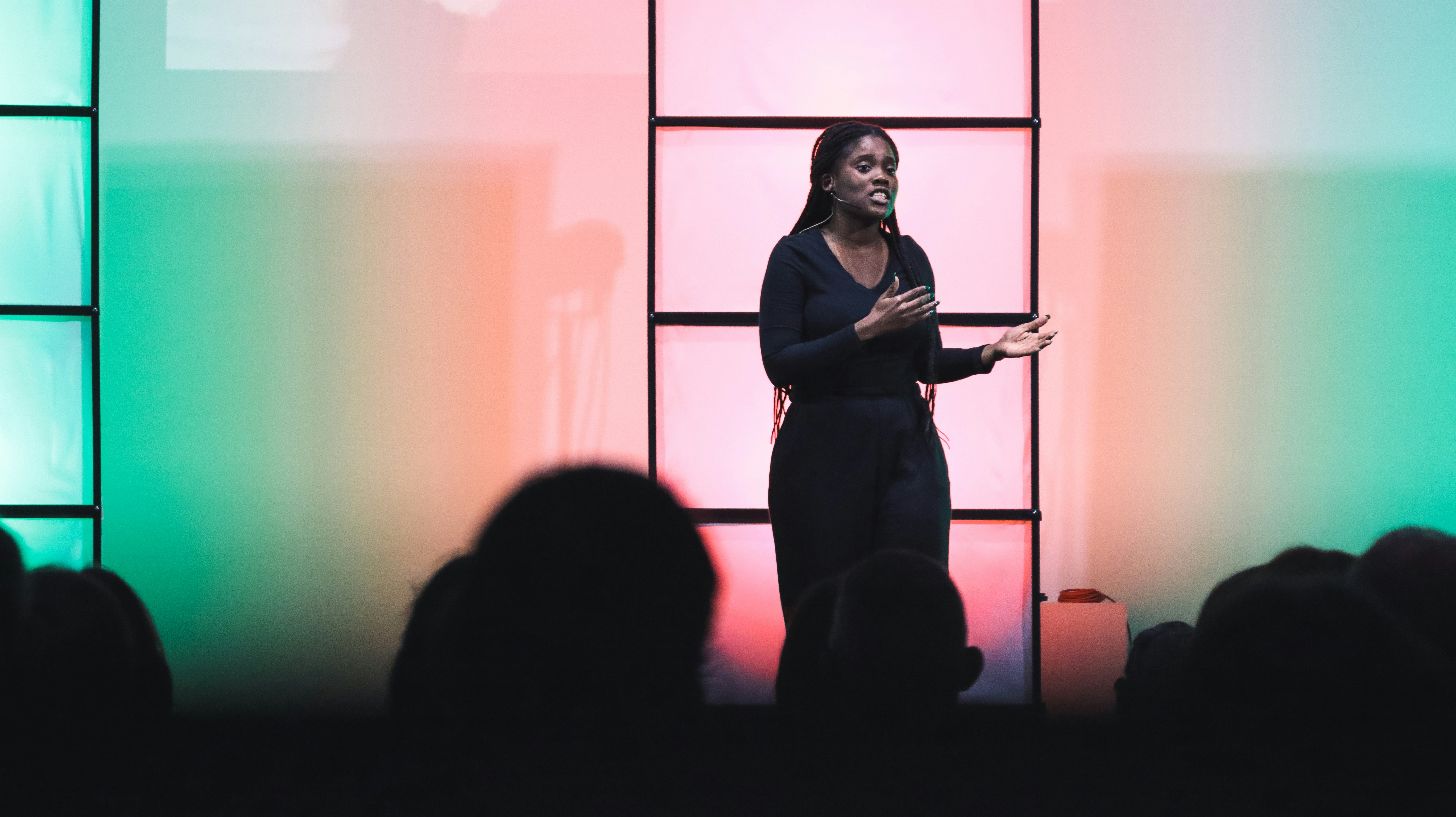
How to Present Semiconductor Solutions to Non-Technical Audiences: A Public Speaking Guide for Job Seekers
Semiconductors are the foundation of modern technology—from smartphones and solar panels to EVs and medical devices. But as the industry grows in complexity and global importance, the ability to communicate how these technologies work—and why they matter—has never been more essential. For job seekers in the semiconductor sector, clear communication is now a vital soft skill. Whether you're an engineer, researcher, product manager, or commercial specialist, your ability to explain semiconductor solutions to non-technical stakeholders can set you apart in job interviews and on the job. This guide will show you how to structure your presentations, simplify technical content, design effective visuals, and confidently address tough stakeholder questions in a way that builds trust, clarity, and impact.
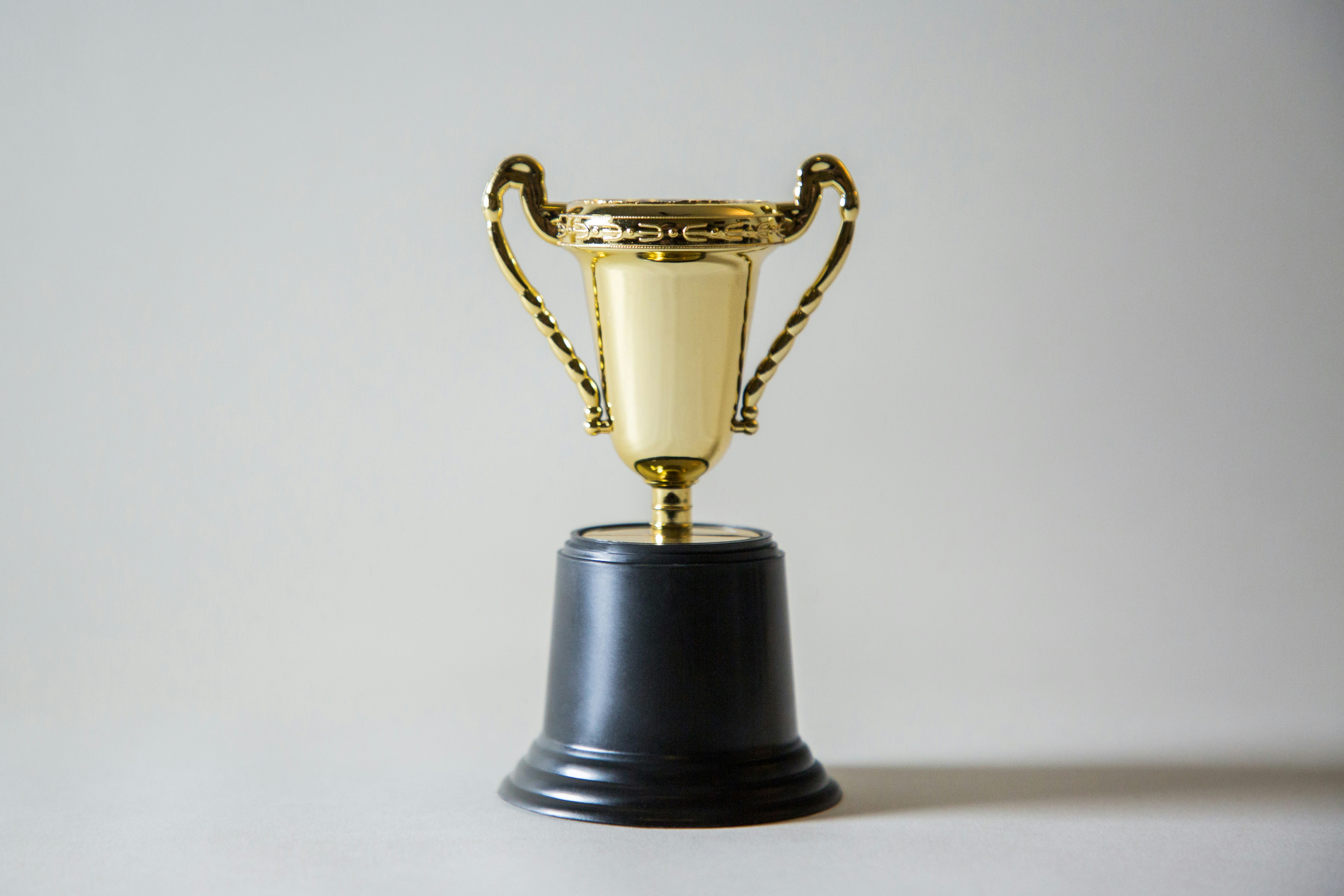
Semiconductor Jobs UK 2025: 50 Companies Hiring Now
Bookmark this guide—refreshed every quarter—so you always know who’s really expanding their semiconductor design, fabrication & equipment teams. The UK’s new Semiconductor Strategy (£1 billion over ten years), a wave of chip‑supply onshoring and record venture funding for compound semiconductors mean demand for design engineers, process‑integration scientists, test & yield specialists, EDA developers and field‑service engineers is soaring in 2025. Below are 50 organisations that have posted UK‑based semiconductor vacancies or announced head‑count growth during the past eight weeks. They’re grouped into five easy‑scan categories. For every employer you’ll see: Main UK hub Example live or recent vacancy Why it’s worth a look (technology node, culture, mission) Search any company on SemiconductorJobs.co.uk to view current ads, or set up a free alert so fresh openings land straight in your inbox.
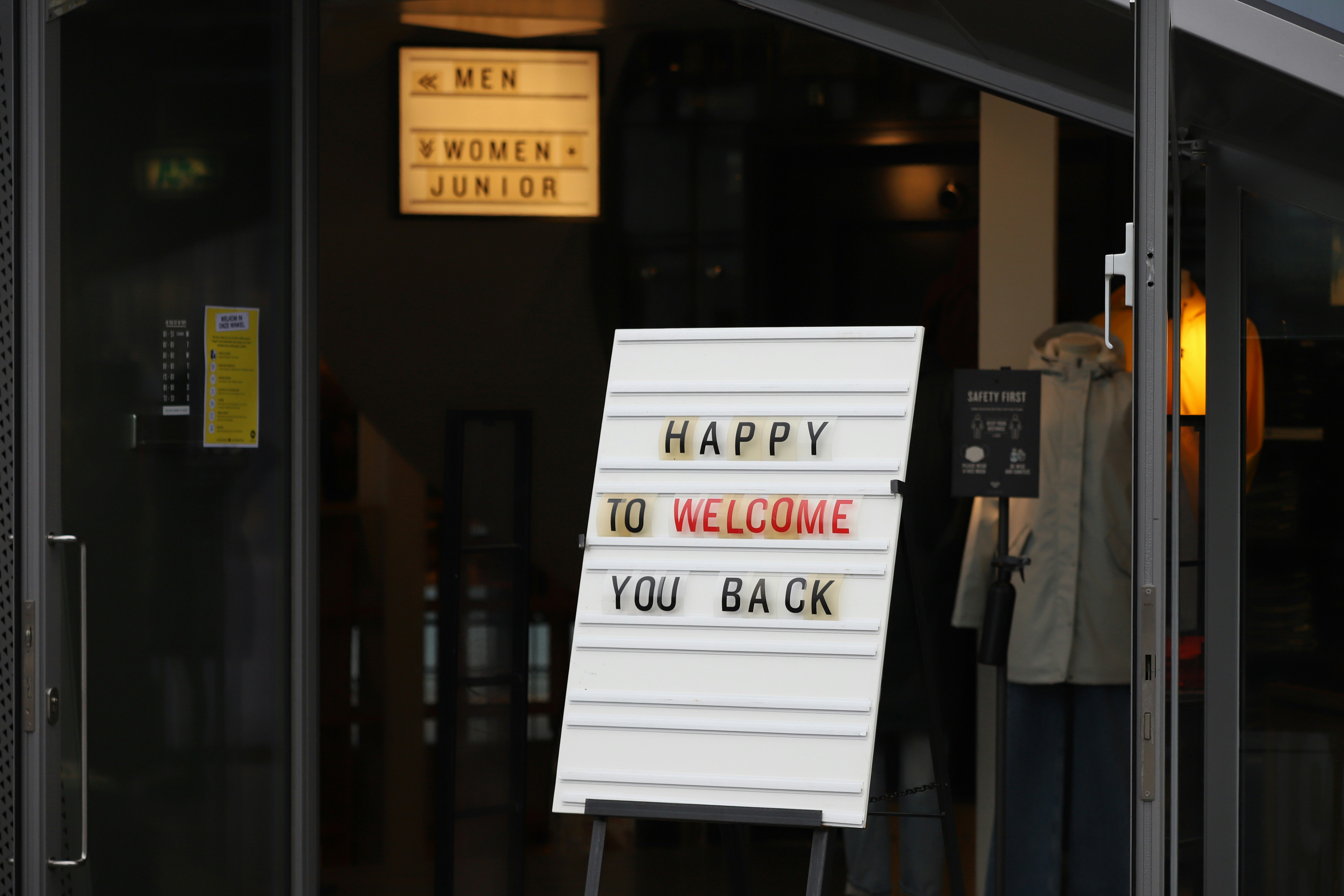
Return-to-Work Pathways: Relaunch Your Semiconductor Career with Returnships, Flexible & Hybrid Roles
Re-entering the workforce after a career hiatus can feel like manufacturing a new wafer—high-precision and potentially daunting. In a specialised field such as semiconductors, where process nodes shrink and technology evolves rapidly, parents and carers returning to work need both technical refreshers and flexible arrangements. Fortunately, the UK’s semiconductor sector now offers a variety of return-to-work pathways—from structured returnships to flexible and hybrid roles. These programmes value the transferable skills you’ve gained, pairing you with mentorship, targeted upskilling and supportive networks to ease your transition back into chip design, fabrication, test or equipment engineering. In this guide, you’ll discover how to: Understand today’s UK semiconductor landscape Leverage your organisational, communication and resilience skills in semiconductor roles Tackle common re-entry challenges with practical solutions Refresh your technical and process knowledge through targeted learning Access returnship and re-entry programmes tailored to semiconductors Find roles that fit around family commitments—whether flexible, hybrid or full-time Balance your career relaunch with caring responsibilities Master applications, interviews and networking in the semiconductor industry Draw inspiration from real returner success stories Get answers to frequent questions in our FAQ section Whether you’re aiming to return as a process engineer, circuit designer, test development engineer or equipment specialist, this article maps out the steps and resources you need to reignite your semiconductor career.