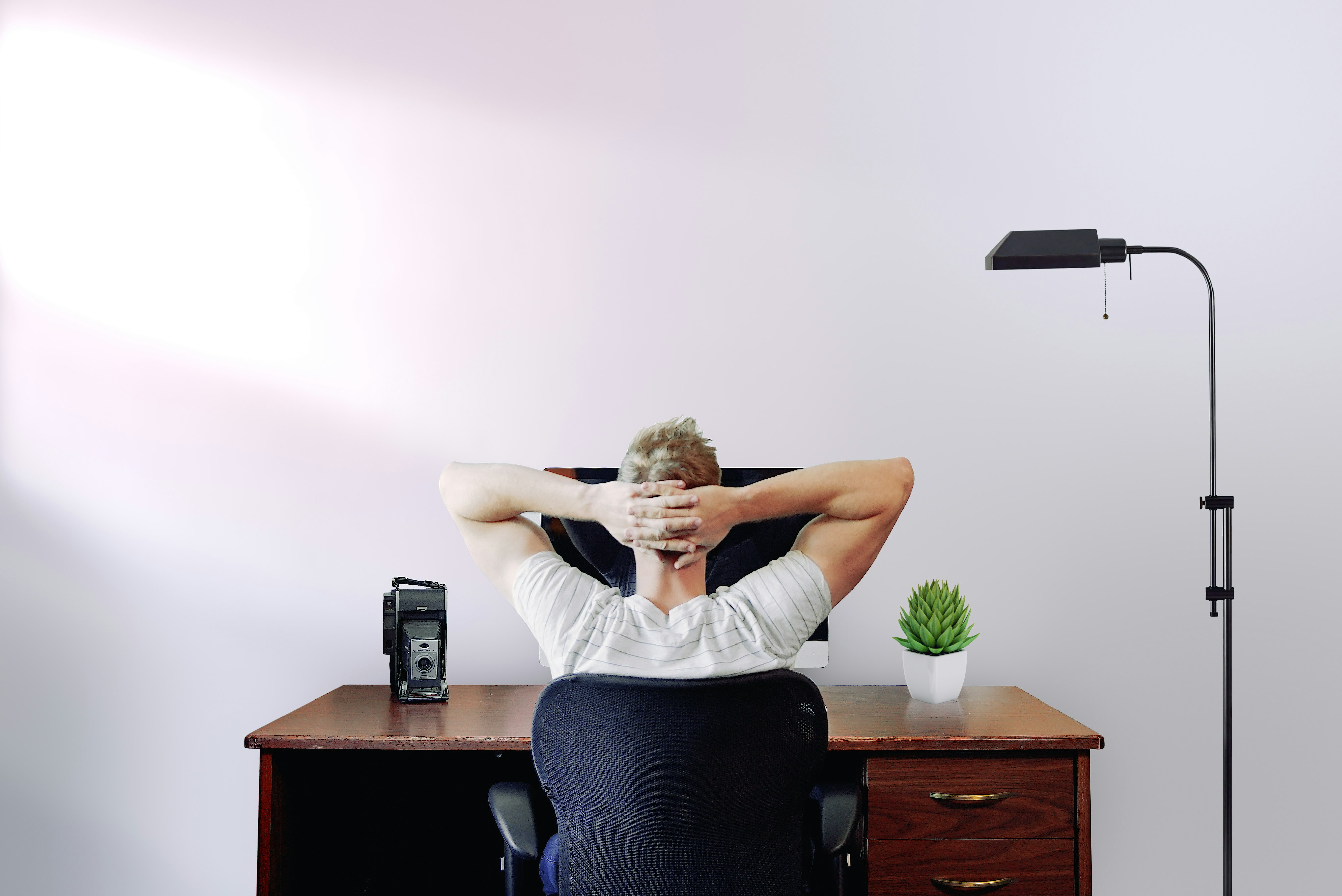
How to Achieve Work-Life Balance in the Semiconductor Industry: Practical Strategies for Thriving in a Cutting-Edge Field
Semiconductors form the invisible backbone of modern technology—powering everything from smartphones and medical devices to electric vehicles and advanced computing systems. As global demand for microchips continues to surge, the semiconductor industry finds itself racing to innovate, ramp up production, and handle ever-evolving challenges around miniaturisation, energy efficiency, and supply chain constraints. These pressures create a high-stakes, fast-paced environment, where engineers, designers, supply chain managers, and countless other professionals can feel stretched thin.
Yet, amid the hustle of tight production timelines, intricate design cycles, and competitive R&D projects, a pressing question arises: Is it possible to strike a meaningful balance between the demands of semiconductor roles and a fulfilling personal life? The short answer is yes—provided you adopt clear boundaries, realistic planning, and self-care practices that safeguard your well-being.
This article offers a comprehensive look at:
Why semiconductor jobs can become especially intense and demanding.
Strategies for setting realistic expectations among stakeholders and colleagues.
The vital role of mental health in sustaining high performance over time.
Practical tips to protect personal time, even when deadlines loom.
How employers can foster supportive cultures where innovation coexists with a healthier work-life blend.
Whether you’re a process engineer fine-tuning wafer fabrication, a device designer tackling next-generation transistors, or a supply chain specialist juggling global logistics, these insights will help you navigate the semiconductor field’s complexities without sacrificing your personal well-being.
1. The Evolving Landscape of Semiconductors
In recent years, the semiconductor sector has been catapulted into the spotlight due to technological advances and global chip shortages. Professionals across the industry face escalating demand for more powerful, smaller, and energy-efficient chips to support a new wave of applications such as:
5G and Beyond
Next-generation wireless networks hinge on advanced RF components, driving heavy R&D in semiconductor design and manufacturing.Artificial Intelligence and Machine Learning
Compute-intensive AI workloads necessitate specialised hardware like GPUs, ASICs, and neuromorphic chips—pushing the boundaries of speed, parallelism, and heat dissipation.Electric and Autonomous Vehicles
Automotive semiconductors must withstand harsh operating conditions while delivering real-time performance for driver-assist systems and EV powertrains, adding layers of complexity to design and testing.IoT and Edge Devices
Smart devices for homes, cities, and industrial settings rely on robust, low-power semiconductors to function reliably at scale, often requiring “always-on” designs with minuscule energy footprints.Advanced Packaging and 3D Integration
As conventional scaling hits physical limits, chipmakers seek to stack, package, and interconnect multiple dies in innovative configurations, leading to new manufacturing flows and quality checks.
Given this accelerating pace, it’s hardly surprising that semiconductor professionals often grapple with high-intensity roles—whether they’re pushing yield improvements, verifying complex designs, or expediting product ramps.
2. The Reality of High-Intensity Roles
Why does working in semiconductors frequently feel like navigating a never-ending sprint? A few contributing factors stand out:
2.1 Complex Manufacturing Processes
Fabrication lines for advanced nodes (e.g., 7 nm, 5 nm, or even 3 nm) involve dozens—sometimes hundreds—of intricate steps. Minor errors in lithography, doping, or etching can ruin entire wafer batches, generating intense pressure to constantly monitor and refine processes.
2.2 Global Supply Chain Constraints
From raw materials and equipment to distribution networks, semiconductor supply chains span multiple continents. Disruptions—be it a natural disaster or geopolitical event—can trigger urgent redesigns or logistics gymnastics. Professionals may find themselves tackling overnight calls or weekend shifts to keep shipments on track.
2.3 Rapid Product Lifecycles
Semiconductor technologies evolve quickly to maintain performance gains and meet market demands. Engineers and managers often juggle multiple product generations or upgrade cycles concurrently, leaving little breathing room between major project milestones.
2.4 High Capital Investments
Establishing or upgrading a fab is a capital-intensive exercise measured in billions of dollars. Firms pressure teams to optimise yield, reduce time to market, and rapidly recoup investments—amplifying the sense of urgency in day-to-day tasks.
2.5 Stringent Quality and Safety Standards
Semiconductors destined for automotive, aerospace, or medical applications can’t afford reliability flaws. Continuous testing, validation, and compliance protocols introduce extra project layers that must be meticulously managed, often leading to additional stress and longer hours.
All these factors can fuse into a demanding work culture where professionals may feel that stepping away—even briefly—risks falling behind. Yet, setting boundaries and calibrating expectations can help. Let’s look at how.
3. Setting Realistic Expectations
High-pressure environments don’t automatically doom you to perpetual overwork—if you take proactive steps to align stakeholders and manage project scope. Here’s how:
3.1 Transparent Communication
Early in a development cycle or manufacturing run, openly discuss capacity limits and potential bottlenecks. If a product manager envisions a compressed tape-out schedule, highlight technical complexities or compliance steps that require adequate lead time. This candour reduces last-minute panics that can devour personal hours.
3.2 Defining Roles and Responsibilities
Complex semiconductor projects merge multiple domains—circuit design, process engineering, packaging, testing, and more. Vague role delineations often mean certain people pick up “extra” tasks. Clarifying responsibilities ensures each team member understands their workload and avoids chaos.
3.3 Realistic Timelines
One misstep in wafer fab can cascade into multi-day or multi-week delays. Propose buffer periods in your Gantt charts for unexpected issues—like yield fluctuations or equipment downtime—preventing your schedule from becoming unmanageable the moment something goes awry.
3.4 Incremental Milestones
Rather than saving all testing or validation for the end, break your project into smaller checkpoints. Early prototype validation or limited-volume runs allow for iterative adjustments, preventing a single “crunch period” at the tail end that demands round-the-clock efforts.
3.5 Educate Stakeholders on Semiconductor Nuances
Not every collaborator or executive appreciates the intricacies of wafer-level packaging or sub-nanometer lithography. Offer brief explanations of potential hurdles—like contamination risks or complex mask sets—so they grasp why certain tasks can’t be rushed without risking expensive failures.
By setting achievable goals and explaining constraints, you carve out space for methodical progress that doesn’t constantly infringe on nights and weekends. Another important dimension is mental health, which we’ll address in the next section.
4. The Importance of Mental Health
A thriving semiconductor career demands stamina and attention to detail—qualities easily depleted by chronic stress or burnout. Safeguarding mental health isn’t just about personal well-being; it also fuels creativity, error-free execution, and better team dynamics.
4.1 Early Burnout Indicators
Burnout typically appears gradually. Watch for lingering fatigue, irritability, or waning enthusiasm for tasks once enjoyed. In semiconductor contexts, repeated oversights in calculations or test planning can also flag that you’re running on empty.
4.2 Coping with High-Stakes Incidents
When yield dips or a critical design fails final verification, the entire team can feel pressure to fix it immediately. In these tense moments, a culture of collaborative problem-solving—rather than blame—helps preserve morale and fosters a healthier approach to crisis resolution.
4.3 Peer Communities and Support
Semiconductor professionals often find solace in internal Slack channels or external forums dedicated to design verification, packaging, or manufacturing. Sharing experiences with peers who’ve faced similar wafer-level challenges or supply chain snags can normalise difficulties and provide practical fixes.
4.4 Integrating Self-Care Routines
Short mental resets—like a walk outside, a mid-shift stretch, or a quick mindfulness exercise—maintain focus during extended test cycles or data analysis sprints. Over time, these micro-breaks improve mental clarity and reduce mistakes that might otherwise occur when you’re overstressed.
4.5 Tapping Organisational Resources
If your company or team provides mental health benefits, stress management workshops, or an Employee Assistance Programme (EAP), take advantage. Engaging with these resources—even preemptively—reinforces that mental wellness is a baseline requirement, not an optional luxury.
With mental resilience as a foundation, you’ll be better equipped to practice day-to-day habits that safeguard your personal life. Next, let’s delve into practical strategies you can apply immediately.
5. Practical Strategies for Achieving Work-Life Balance
Balancing complex wafer fabrication or device development with personal obligations demands consistent effort. These tangible methods can help re-establish control and protect your downtime.
5.1 Structured Time Blocking
Focus Windows: Reserve uninterrupted blocks—say, two-hour intervals—to tackle high-priority tasks such as layout revisions or test data analysis. Inform colleagues that you’ll check messages only after completing deep work.
Administrative Bundling: Designate separate time slots for emails, scheduling, and quick queries. This approach limits context switching, reducing fatigue and mistakes.
5.2 Defining “Off-Hours”
Clear Cutoffs: If you’re not on-call, set an end-of-day boundary—e.g., 7 p.m.—for addressing non-critical matters. Let your team know that unless there’s an emergency (like a major yield drop), you’ll handle other issues tomorrow.
Notification Management: Adjust phone or email settings to mute routine alerts during personal time, focusing only on major triggers, such as a critical equipment failure or essential security breach.
5.3 Leveraging Remote or Flexible Schedules
Work from Home Options: While semiconductor work often requires lab or fab visits, some tasks—like design simulations, data analysis, or documentation—can be done remotely. Flexible arrangements help reduce commute-related stress and allow you to fit personal errands or family duties into your schedule.
Shift or Rotation Systems: For lines running 24/7, a well-structured rotation ensures no single engineer or manager perpetually bears weekend or overnight responsibilities. Spread the load fairly to maintain morale.
5.4 Physical and Mental Wellness Routines
Micro-Breaks: Every hour or two, stretch, hydrate, or take a brief walk to reset your posture and mental acuity. Over a 12-hour shift, these short respites accumulate into a measurable wellness boost.
Exercise and Nutrition: Setting a consistent workout schedule—even 20 minutes of exercise daily—supports stress management, better sleep, and resilience. Balanced meals (versus quick junk-food fixes) sustain energy during demanding tasks.
5.5 Scheduling Personal Commitments
Treat Leisure as Non-Negotiable: Slot personal hobbies, family time, or relaxation into your calendar with the same seriousness as project meetings. Blocking these periods prevents them from getting overridden by unplanned tasks.
Plan for Unexpected Overtime: Keep some flexibility around key milestones. If you suspect the final test for a new process might spill over into the weekend, arrange personal activities for earlier or later, so you aren’t left scrambling.
Implementing these strategies consistently helps you stay engaged at work and truly disconnect during off-hours. And remember, organisational culture is critical. Let’s see how employers can promote a healthier environment.
6. The Role of Employers and Industry Leaders
Employees’ personal efforts go further when supported by policies, resources, and a leadership ethos that values sustainable work habits. In the semiconductor realm, that means:
6.1 Open Communication Channels
Managers and team leads should conduct regular check-ins to gauge workload, highlight potential roadblocks, and gather feedback on timeline feasibility. Addressing small concerns early prevents them from turning into major crises that demand last-minute heroics.
6.2 Flexible and Equitable Scheduling
Not all tasks need to be bound to traditional 9-to-5 blocks. If employees work best early in the morning or prefer a split schedule for child care, accommodate them where practical. Similarly, rotate heavier demands—like final product validation—rather than letting the same people shoulder them repeatedly.
6.3 Clear Role Definitions and Collaboration Structures
Well-documented project plans and job scopes reduce confusion. This clarity ensures that if, for instance, a tool fails in the fab, the correct engineer or technician is alerted—not half the team. Organisational structures that spell out who’s in charge of each product stage avoid duplication and unbalanced workloads.
6.4 Training and Development During Work Hours
The push toward smaller nodes or advanced packaging can require new skill sets—like EUV lithography or fan-out wafer-level packaging. Encouraging on-the-clock training acknowledges the complexity of your field while preventing staff from sacrificing personal time to stay current.
6.5 Normalising Well-Being Initiatives
When leaders openly take days off, attend stress-management workshops, or emphasise mental health resources, it breaks the stigma around self-care. By demonstrating that recharging is part of high performance—not an obstacle to it—companies retain motivated teams over the long haul.
With these frameworks in place, semiconductor professionals can engage in meaningful work and maintain personal stability. As technology advances, additional shifts may also help reduce the industry’s pressure cooker effect—our next topic.
7. The Future of Work-Life Balance in the Semiconductor Sector
The semiconductor ecosystem won’t stand still. Emerging trends could reshape working conditions, potentially easing some of the traditional constraints.
7.1 Automated Manufacturing and AI-Driven QC
As robotics, process automation, and AI algorithms become more prevalent in fabs, human oversight might shift to more strategic roles—reducing manual grunt work and late-night reconfigurations. AI-based defect analysis could preempt yield issues before they cause entire line disruptions.
7.2 Greater Emphasis on Supply Chain Resilience
Ongoing chip shortages have taught valuable lessons about the fragility of global supply lines. Investments in local production and diversified sourcing can lead to more stable planning horizons, minimising reactionary schedule changes.
7.3 3D Integration and Advanced Packaging Innovations
Techniques like chip stacking and integrated fan-out packaging, if standardised, could streamline certain product cycles by reducing the need for multiple separate assemblies. While complex, once these methods mature, they might shorten total design-to-market timelines—and the associated crunch.
7.4 Collaborative Ecosystems and Open Standards
Semiconductor players, including foundries, EDA software vendors, and device manufacturers, are increasingly cooperating on open specifications. These shared frameworks could reduce the overhead of proprietary workflows, simplifying design exchange and possibly lowering last-minute integration headaches.
7.5 Workforce Shifts Toward Sustainability and Flexibility
Younger professionals often prioritise work-life balance, mental health, and environmentally responsible practices. As they become leaders, the industry could pivot toward more flexible norms—like hybrid schedules, mental health breaks, or extended parental leave—embedding well-being as a pillar of operational excellence.
Collectively, these trends hint at a semiconductor future that retains its dynamism yet evolves to respect the people behind each wafer run or design iteration. In our final section, we’ll wrap up the key messages on building a robust yet balanced career in this field.
8. Conclusion: Balancing Innovation and Personal Well-Being in Semiconductors
Is work-life balance truly viable in a sector where microseconds and nanometres make or break success? Absolutely—if you combine strategic boundary-setting, consistent self-care, and supportive organisational frameworks. While semiconductors will always present unique demands—be it from advanced lithography or complex supply chains—these pressures don’t have to overshadow personal fulfilment.
Key Takeaways
Understand the Landscape
Recognise how advanced process nodes, R&D intensity, and global supply logistics contribute to a high-pressure environment.Set Manageable Expectations
Transparent dialogue with stakeholders, role clarity, and realistic timelines reduce last-minute crunches.Prioritise Mental Health
Proactively guard against burnout by leveraging resources, taking breaks, and building community support.Use Practical Work Routines
Time blocking, offline hours, remote options, and personal scheduling keep stress in check while maintaining productivity.Champion Organisational Change
Leadership that invests in flexible policies, fair rotations, and training fosters a culture where professionals can thrive long-term.
Ready to explore semiconductor jobs with a forward-thinking approach to both technology and well-being? Visit www.semiconductorjobs.co.uk to find roles that align with your passion for miniaturisation, circuit design, or process engineering—while still valuing work-life balance. From global chip manufacturers to specialised fabless start-ups, these opportunities enable you to shape the future of electronics without surrendering your personal life to perpetual deadlines.
Disclaimer: The information here is for educational and informational purposes only. It does not replace professional advice regarding career decisions, mental health, or legal matters. Always consult qualified specialists for personalised guidance.